PET bottle preform injection mold: lip (mouth)
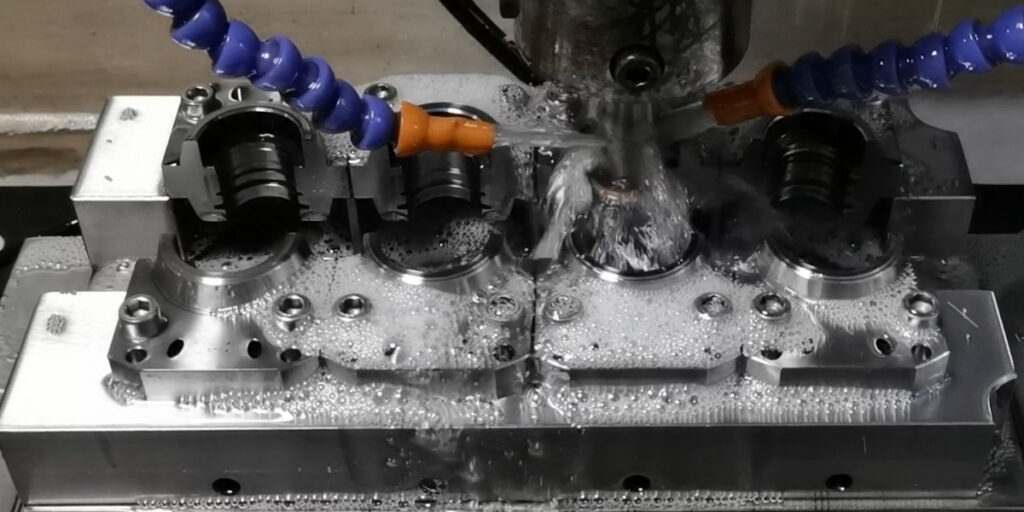
Advantages of Spark Machine Tapping
Spark machine tapping is a category of spark machining, also known as electrical discharge tapping. It is a controllable electrical discharge machining technology that uses high-frequency voltage to discharge pulse currents, forcing them to break through the surface of the processed material through electrodes and form tiny discharge channels, achieving the purpose of machining.
The working principle of spark machine tooth tapping is mainly based on the thermal and mechanical effects during the process of electric spark discharge. The thermal effect refers to the conversion of electrical energy into thermal energy during the process of electric spark discharge, causing the material on the surface of the workpiece to melt and gasify. The generation of thermal energy mainly depends on the discharge energy density and discharge time of electric sparks. The mechanical effect refers to the impact force and thermal energy generated during the electrical discharge process, which can cause elastic and plastic deformation of the surface material of the workpiece, resulting in the formation of pits.
The process of tapping teeth with a spark machine includes the following steps:
1. Apply high voltage pulses between the tool electrode and the workpiece;
2. The gap between the tool electrode and the workpiece generates electric sparks;
3. The impact force and thermal energy generated by electric spark explosions melt and gasify the material on the surface of the workpiece;
4. The melted and gasified materials are quickly thrown out, forming pits;
5. By controlling the frequency, amplitude, and feed rate of the tool electrode, the machining depth and surface roughness can be precisely controlled.
The generation of tooth tapping impact force mainly relies on the explosive force of electric sparks and the hydrodynamic effect. Toothtapping is widely used in aerospace, automotive manufacturing, mold manufacturing, medical equipment and other fields. In these precision machining fields, spark machine tapping has improved machining efficiency and accuracy compared to traditional machining methods, reduced cutting force and vibration, and improved the quality and reliability of parts.